Digital transformation market size is projected to reach USD 8.92 trillion by 2030, at a CAGR of 21.6%, as per Fortune Business Insights. Digital Transformation and Industry 4.0 are revolutionizing the manufacturing landscape, ushering in an era of unprecedented innovation and efficiency. Their synergy is reshaping traditional manufacturing paradigms, offering a glimpse into a future where smart factories and data-driven decision-making redefine the industry.
What is Industry 4.0?
Industry 4.0 encapsulates the fourth industrial revolution, signifying the convergence of physical and digital technologies revolutionizing manufacturing. Also known as the Internet of Things (IoT), smart manufacturing, or digital manufacturing, it relies on digital transformation. This entails integrating digital transformation services across business areas, instigating fundamental operational changes and cultural shifts. The integration of digital technologies is pivotal in fostering unprecedented agility, efficiency, and quality in manufacturing, ushering in a new era of innovation in the sector.
Did you know?
Coined in 2011 by German academics, the term Industry 4.0 has emerged as the predominant framework for the fourth industrial revolution, signifying the fusion of physical and digital technologies in manufacturing. Often dubbed the “smart factory” or the “factory of the future,” Industry 4.0 revolutionizes manufacturing through enhanced data-driven decision-making, increased customization, and accelerated production times.
Key Technologies Fueling Manufacturing Industry’s Digital Transformation
Internet of Things (IoT)- An integral element of smart factories, the IoT involves machines on the factory floor equipped with sensors, featuring IP addresses for web-enabled connectivity. This connectivity enables the collection, analysis, and exchange of substantial amounts of valuable data.
Cloud Computing- A cornerstone of Industry 4.0 strategies, cloud computing facilitates connectivity and integration across various business units. It efficiently processes and analyzes large datasets, reducing startup costs for small- to medium-sized manufacturers who can scale their needs as the business expands.
Data Traceability- Data traceability, achieved through unique identifiers like barcodes and RFID tags, enables manufacturers to monitor a product’s journey, ensuring effective supply chain management, regulatory compliance, and streamlined recalls.
AI and Machine Learning- AI and machine learning unlock the potential of vast information generated not only on the factory floor but across business units and external sources. These technologies provide insights for visibility, predictability, and automation of operations. For instance, predictive maintenance based on machine learning algorithms enhances uptime and efficiency.
Edge Computing- Real-time production demands data analysis at the “edge” where it is created to minimize latency. Edge computing ensures near-real-time responses, critical for addressing safety or quality issues promptly. Keeping data near its source reduces security risks and reliance on network reliability.
Cybersecurity- Critical in Industry 4.0, cybersecurity protects against malicious attacks. The connectivity enabling efficient processes also exposes vulnerabilities. A comprehensive cybersecurity approach, covering both IT and OT equipment, is crucial during the digital transformation.
Digital Twin- Industry 4.0’s digital transformation enables the creation of digital twins—virtual replicas of processes, production lines, and supply chains. Data from IoT sensors and devices form these twins, aiding in productivity, workflow improvement, and new product design. Manufacturers simulate processes to minimize downtime and enhance capacity.
Other Advanced Manufacturing Technologies
3D Printing-Used for on-demand prototype and part creation, 3D printing reduces lead times and enables product customization.
Additive Manufacturing- This method constructs parts and products from raw materials, allowing the production of intricate geometries not feasible with traditional methods.
Digital Twinning- Creating virtual models of physical systems, digital twinning helps manufacturers test and optimize processes before implementation on the shop floor.
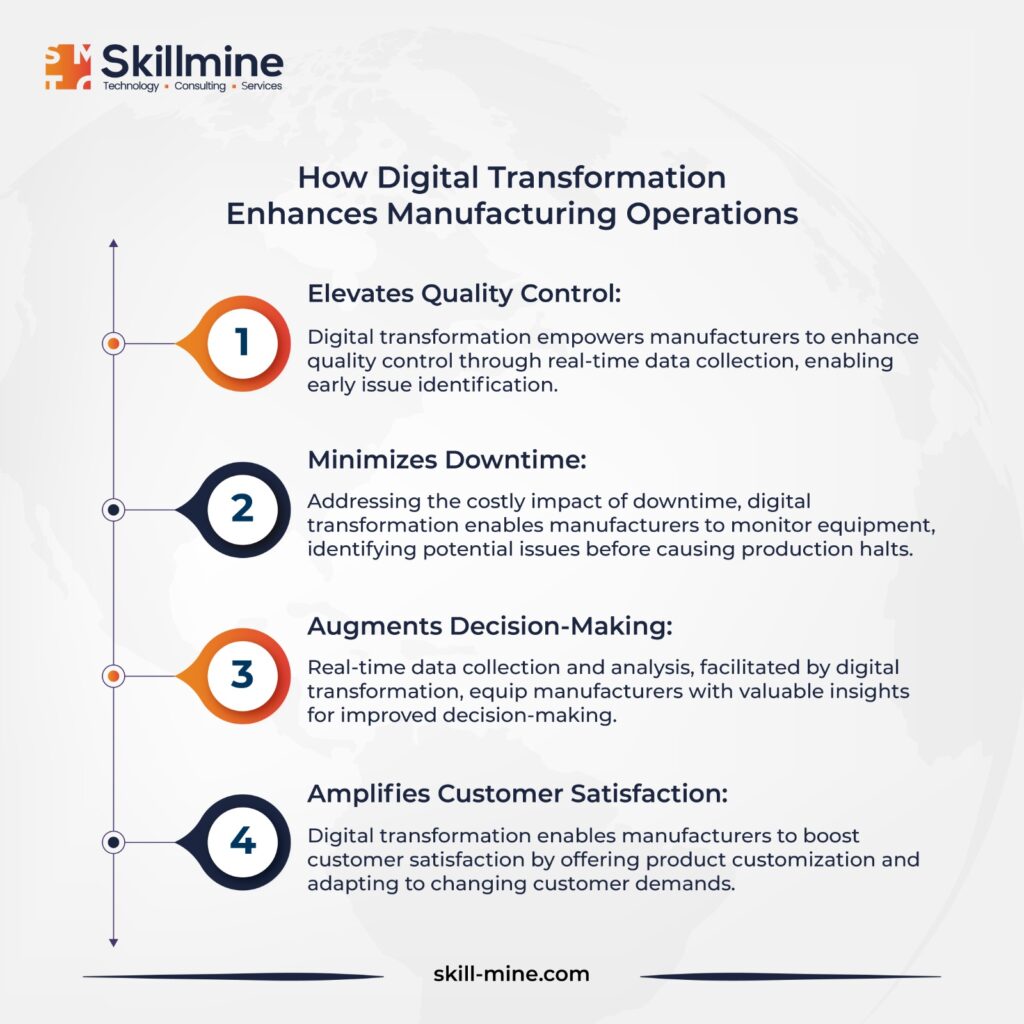
Conclusion
Industry 4.0 in manufacturing is propelled by digital transformation. Collaborating with engineering teams, manufacturers leverage digital technologies to connect systems, analyze real-time data, enhance decision-making, and optimize operations. The outcome is a more agile, responsive, and efficient manufacturing sector adept at meeting the demands of the digital era. Skillmine’s digital transformation solutions synchronize your business requirements with suitable technology to craft an ideal solution aimed at optimizing operational efficiencies.
Looking for expert technology consulting services? Contact us today.